Abstract: This article describes the application of valve grinding technology in nuclear power maintenance and the importance of grinding technology for valve maintenance. The article discusses the problem of valve grinding from the aspects of control of valve grinding, grinding tools and materials, attention points in grinding, and inspection of valve sealing after grinding, and thus provides certain reference value for improving valve grinding quality and work efficiency.
Key words: nuclear power plant; valve grinding; maintenance; sealing inspection 0 Introduction Valves are an indispensable part of the safe operation of a nuclear power plant. Nearly every system of a nuclear power plant is inseparable from a valve. Taking a pressurized water reactor nuclear power plant with two million-kilowatt units as an example, the number of valves is about 30,000. These valves are distributed in various systems of nuclear power plants, and some of the important valves such as main steam isolation valves and regulators are safe. Valves and main steam safety valves, as well as various nuclear-grade valves used in a one-loop system, are directly related to the normal and safe operation of nuclear power plants, and their reliability does not allow any errors. According to the IAEA nuclear power station accident case, the valve accounts for a significant proportion of the shutdowns, shutdowns, and even nuclear leaks caused by valve failures and failures. Therefore, the valve plays an extremely important role in the safe and reliable operation of the power station.
Random group long-term operation, all kinds of valves through the operation of extrusion, cold and heat change, fluid erosion, ionization and other factors, will cause the phenomenon of the original sealing effect can not be achieved, then you need to valve and valve The seat's sealing surface is ground or polished to restore optimal sealing and design levels. In the process of valve repair, most of the maintenance procedures and processes can be controlled by the requirements of the regulations. Only the grinding of the sealing surface is difficult to carry out effective control due to the absence of suitable measuring tools. The need to rely on the staff's skills and experience to ensure quality, so valve grinding is a heavy point in the valve maintenance activities.
1 Valve Grinding The valve is ground to repair the damaged sealing surface of the valve and restore it to a good sealing effect. Power plant valve seals are generally used for surface sealing and wire sealing. To improve the quality of grinding, we must first understand the quality control requirements of the grinding process. On the other hand, it is necessary to clarify the factors that affect the sealing and the corresponding inspection methods.
2 The main factors affecting the seal For the face seal grinding, it mainly controls the four factors of flatness, angle, roughness and sealing specific pressure. A good flatness means that the sealing surface has no abnormal defects such as depressions, protrusions or scoops; the angle of the sealing surface also plays a decisive role, in particular the wedge valve requires the highest angle; good roughness can make the sealing effect better; sealing specific pressure The pressure on the sealing surface, in the case of pressure determination, depends on the area of ​​the sealing surface, so it is necessary to measure the width of the sealing surface after grinding.
For wire seal grinding, the four factors of concentricity, roundness, angle, and strength are mainly controlled. The concentricity of the valve stem, valve disc and valve seat will affect the fitting of the valve stem and the valve seat, so that the sealing surface is uneven in the circumferential direction, there may be a certain sealing force of the sealing surface exceeds the allowable sealing pressure ratio. The sealing surface is damaged, and at the same time, the sealing force of some other part cannot reach the specific pressure, resulting in internal leakage. The seal face of the wire seal can be seen as the overlap of the two circles on the disc and the seat, and it is important to position the stand when grinding or machining.
3 The selection of tools and consumables commonly used grinding machine sub-pneumatic, electric two, usually nuclear island repair selection electric grinder to prevent dust pollution. Hand-grinding requires the use of a special grinding tool according to the type and size of the valve.
In nuclear power overhaul, abrasive sandpaper with higher quality is usually selected as abrasive material. For some equipment with special requirements, abrasives and other abrasives are selected depending on the actual situation. The choice of the texture of the abrasive depends mainly on the material of the sealing surface to be ground. For example, when the sealing surface is made of cast iron, brass, copper, aluminum, non-metallic materials, etc., the abrasive material of silicon carbide is usually used; the sealing surface is stainless steel, tool steel For materials such as ceramics and ceramics, abrasives with diamond texture should be used. The choice of abrasive grain size is based on the surface roughness requirements of the sealing surface, such as grain size 60–180 for rough grinding (Ra ≤ 0.8) and 220–400 for fine grinding (Ra ≤ 0.4). The particle size selected for polishing (Ra ≤ 0.1) is 500-1200.
4 Hand-grinding manual grinding is mainly used for stop valves, safety valves and gate valves and check valves with small diameters. It is required for staff with high requirements and requires certain experience.
Due to the inconsistent degree of defect between valve disc and valve seat, it is not possible to directly use valve discs and valve seats to grind. It is necessary to make corresponding special tools (benchware) according to the type and diameter of the valve. For parts that do not require special tools, they should be calibrated. Lapping on a qualified grinding plate. In the production of valve seat grinding equipment should pay attention to, the hardness of the material of the tire material should be lower than the hardness of the equipment; Second, according to the size of the valve cavity to make guide positioning parts for guidance, so that the grinding rod does not skew when grinding; for angled The required valve, the angle of the lathe grinding head must be consistent with the angle of the valve body.
Grinding process is usually divided into coarse grinding, fine grinding, polishing and other steps, according to different grinding stages, should use different granularity of sandpaper, abrasive paste for grinding. When grinding, attention should be paid to uniform force. When grinding the valve flap on the grinding plate, it should be rotated in the same direction or grinded with the “8†track.
5 Grinding machine grinding commonly used grinding machine is divided into pneumatic and electric two kinds according to driving mode. The selection of the grinding machine is actually the choice of the performance of the grinding machine. In general, the selection of the grinding machine is determined by the conditions and materials required for grinding the sealing surface. At the same time, the site environment, the valve depth, and the installation manner must also be considered. Normally, electric grinders are used in the grinding work of nuclear islands to reduce the risk of dust diffusion.
5.1 The following points should be noted when grinding with a grinder:
Alignment: For line-sealed valves, the centering of the grinder is relatively easy, and it is usually ensured by a positioning device fitted on the outer surface of the grinder drive rod and the flange of the valve cover.
Leveling: When installing the planet, the leveling of the planets is important. This step is usually performed on a flat plate.
Grinding pressure: Grinding pressure also greatly affects the grinding effect and efficiency.
Grinding speed: The grinding speed has a great influence on the working efficiency. If the speed is too small, it will obviously prolong the grinding time. However, if the speed is too fast, the high temperature generated by the grinding will cause the failure of the grinding wheel and the planetary wheel to stick and cause degumming and damage the sealing surface. .
Observe the grinding situation: This process is more important, but it is easily overlooked. Through this step, you can find out the mistakes of the previous steps in time. Usually, every time you replace the sanding pad, you should observe the sealing surface and the old pad, and adjust the grinding according to the sealing surface.
Replace the abrasive sheet: As the abrasive particles gradually fail with the grinding time, the abrasive sheet needs to be replaced frequently. Before changing the grinding sands for grinding, the sealing surfaces and planet gears must be thoroughly cleaned to remove the particles from the previous grinding.
5.2 Grinding quality inspection For inspection of the sealing surface of the valve after grinding, there are usually three methods: blue oil test, knife-edge inspection, and monochromatic light interference inspection. However, because of the on-site environment and various factors, the blue oil test method is usually used. Checks are performed using a knife ruler if circumstances permit.
5.3 Blue Oil Test The blue oil test is the most widely used sealing surface inspection method because of its easy operation and adaptability to a variety of on-site complex environments. Its purpose is mainly to check the sealing surface of the fit, the need to explain is the blue oil test (some use red powder, phosphor, fluorescent oil, etc.) the thinner the coating the better, blue oil seems simple, in fact It is a test of skill, if the coating is too thick, it is easy to produce erroneous judgments.
5.4 The knife edge ruler uses the knife edge ruler to check the flatness, which is actually the light transmission method. The knife edge of the knife edge is pressed against the sealing surface in the direction of the sealing surface diameter, and the light transmittance of the knife edge portion is observed from the side of the knife edge ruler. If the light passes through the outside of the sealing surface, the sealing surface is convex; if the light Penetration from the inside of the sealing surface indicates that the sealing surface is concave; if no light is transmitted, it indicates that the sealing surface has a good flatness.
5.5 The monochromatic light interference knife edge rule and blue oil test are very practical methods, but these two methods have certain experience requirements for the staff. The monochromatic light interferometry does not appear to affect the judgment of different people, but it can also be quantitatively evaluated. However, this method has a high requirement for the position of the sealing surface. Because most valve seats of the power plant have a narrow gap, and there is no angle for observation, only the test method of blue oil or phosphor powder can be used.
6 Conclusion Valves play a crucial role in the safe operation of nuclear power plants. In particular, the defects of some key valves will directly lead to serious consequences such as shutdowns and nuclear leakage. Therefore, how to ensure the reliability of valves is an important task in nuclear power maintenance. The quality of the grinding in the process of valve repair directly determines the sealing of the valve, and thus affects the reliability of the valve. This article describes the selection of grinding tools and consumables, the standard operation of grinding, and the inspection after grinding, which improves the quality and efficiency of valve grinding technology in nuclear power maintenance applications and provides a more powerful guarantee for the safe operation of nuclear power plants.
references:
[1]Tang Linyan. Analysis of valve manual grinding process [C]//. Annual meeting of Jiangxi Institute of Electrical Engineering, 2014.
[2] Wang Xinjian, Zhang Hongzhuan, Wang Changming, et al. Improvement of Valve Grinding[J]. China Beet & Sugar Industry, 2005(4):54-54.
[3]Wang Jianying,Zhou Zhenxing.A Brief Discussion on the Improvement of Valve Sealing Surface Grinding Method and Tool[J].Inner Mongolia Science Technology and Economy,2002(6):98-98.
Sublimation Protective Paper
Sublimation protective paper is a tool used by sublimation professionals to protect their heat plate and project surface mats from the dye during the transfer process. As a continuous thin paper web used to transport cut-work or roll textile through the heat calander and as a barrier to prevent surplus dye-sub gasses from contaminating the recalculating belt of the rotary calander press.Compatible with ALL oil and electric heated rotary drum calanders. The protective paper is designed to capture all excessive inks transferred through or off the edges of the fabric.
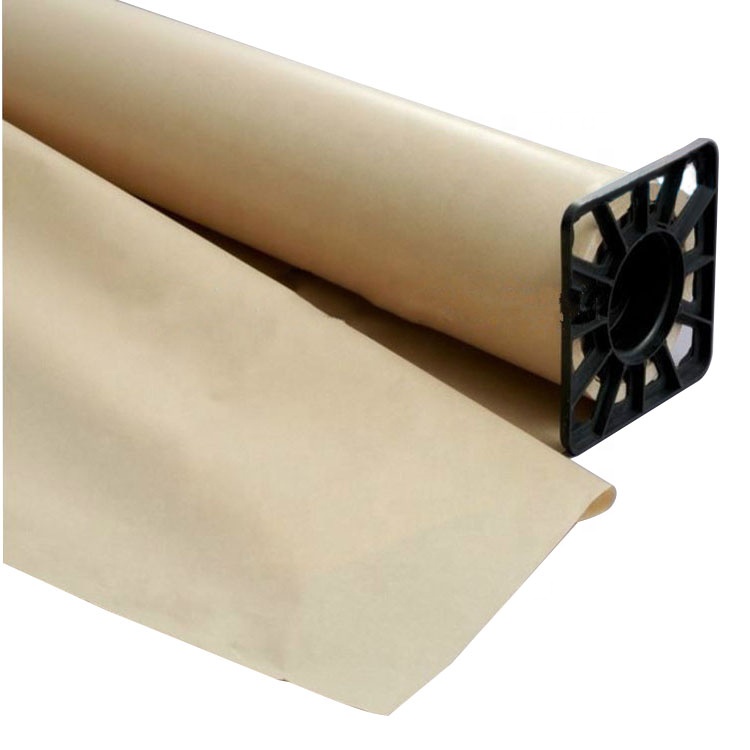
Sublimation Protective Paper,Protective Sheets For Heat Transfer,Heat Press Protective Sheet,Heat Transfer Protective Sheet
CHINAPAPER-ONLINE(SUZHOU) E-COMMERCE CO. LTD , https://www.chinapaper-online.com